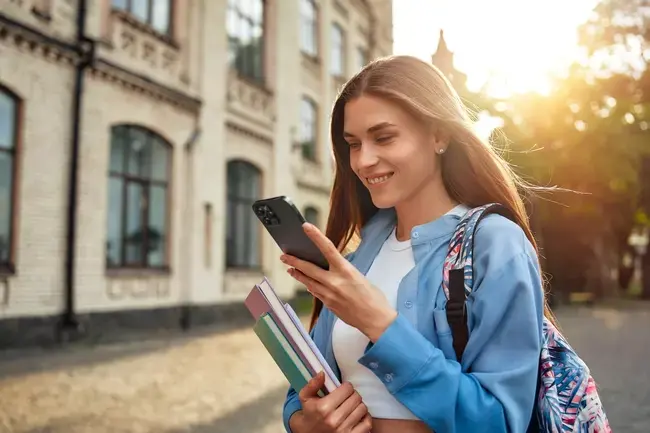
La logística empresarial para mantener el control y planificación es crucial para el éxito de cualquier empresa que maneje productos físicos. Por eso, ya sea que estés trabajando actualmente en el sector logístico o que desees incursionar en esta área, es fundamental conocer los errores más comunes que pueden afectar la eficiencia y efectividad de las operaciones logísticas. Continúa leyendo que te los contamos.
Si no puedes leer el artículo, escúchalo aquí.
Errores más comunes en el control de inventarios
1. Falta de precisión en los registros de inventario
La inexactitud en los registros puede llevar a problemas de abastecimiento y exceso de inventario. Mantener registros precisos es esencial para asegurar que siempre haya suficiente stock disponible sin incurrir en costos innecesarios.
2. No realizar auditorías regulares
Las auditorías periódicas ayudan a identificar discrepancias y mantener la precisión. Sin estas, es fácil que los errores pasen desapercibidos, lo que puede llevar a problemas mayores a largo plazo.
3. Dependencia excesiva en sistemas manuales
Los sistemas manuales son propensos a errores humanos; es mejor utilizar software especializado que automatice el proceso y reduzca la posibilidad de errores.
4. No tener un plan de contingencia
La falta de un plan para situaciones imprevistas puede causar interrupciones significativas. Un buen plan de contingencia asegura que la empresa pueda seguir operando incluso en situaciones adversas.
5. Mala gestión de productos perecederos
No rotar adecuadamente los productos perecederos puede resultar en pérdidas significativas. Es crucial implementar un sistema de rotación de inventarios como FIFO (First In, First Out) que traduce en primero en entrar, primero en salir, es una metodología de gestión de inventarios que asegura que los productos más antiguos se vendan o utilicen antes que los más nuevos.
Este enfoque es especialmente importante para productos perecederos, como alimentos, medicamentos y otros bienes con fecha de caducidad, para minimizar el desperdicio.
<Ya sea que trabajes como planificador de rutas logísticas o en cualquier otro rol de este sector, con una Maestría en Logística Internacional podrás adquirir todos los conocimientos y habilidades que necesitas para evitar estos errores. Haz clic en el botón de WhatsApp y uno de nuestros asesores te brindará toda la información que necesitas para avanzar en tu carrera profesional>.
6. No capacitar al personal adecuadamente
El personal debe estar bien entrenado en procedimientos de control de inventarios. La capacitación continua asegura que todos los empleados estén al tanto de las mejores prácticas y procedimientos actuales.
7. Falta de integración con otros sistemas
La integración con sistemas de ventas y compras es crucial para mantener la coherencia y evitar discrepancias en los datos. Un sistema integrado permite una visión holística de las operaciones de la empresa.
8. No utilizar tecnología de seguimiento
La tecnología como RFID (Identificación por Radiofrecuencia) puede mejorar la precisión y eficiencia del control de inventarios, ya que permite seguimiento en tiempo real de los productos.
9. Mala previsión de la demanda
Otro error que existe en la logística y transporte es no anticipar correctamente la demanda puede llevar a exceso o falta de inventario. Por ello, hay que utilizar herramientas de análisis predictivo para prever la demanda con mayor precisión.
10. No establecer niveles de inventario óptimos
Es importante determinar los niveles adecuados para evitar costos innecesarios y asegurar que siempre haya suficiente stock disponible.
11. Falta de análisis de datos
No analizar los datos de inventario puede impedir la identificación de tendencias y problemas, ya que esto permite tomar decisiones informadas y mejorar la eficiencia operativa.
12. No gestionar adecuadamente las devoluciones
Las devoluciones deben ser gestionadas eficientemente para minimizar el impacto en el inventario. Un proceso bien definido puede reducir las pérdidas y mejorar la satisfacción del cliente.
13. No tener un sistema de clasificación
Otro error que afecta en el control y planificación de la logística empresarial es el hecho de no clasificar los productos según su importancia, ya que esta acción permite mejorar la gestión y priorización de inventarios. Sistemas como ABC (clasificación de inventarios) pueden ser útiles en este aspecto.
14. No realizar mantenimiento preventivo
El mantenimiento de equipos y sistemas es esencial para evitar fallos y asegurar un funcionamiento continuo. Además, puede prevenir problemas antes de que ocurran.
15. Ignorar la retroalimentación del cliente
La retroalimentación puede proporcionar información valiosa para mejorar la gestión de inventarios. Escuchar a los clientes y ajustar los procesos en consecuencia puede mejorar la eficiencia y satisfacción del cliente.
Lee también: ¿Por qué estudiar una Maestría en Logística Internacional?
Problemas logísticos más comunes en un almacén
1. Diseño ineficiente del almacén
Un diseño mal planificado puede dificultar el flujo de trabajo y aumentar los tiempos de manejo. Es importante diseñar el almacén de manera que facilite el acceso rápido y eficiente a los productos.
2. Falta de espacio de almacenamiento
No contar con suficiente espacio puede llevar a la acumulación de productos y desorganización. Optimizar el uso del espacio disponible y considerar soluciones de almacenamiento vertical puede ayudar a mitigar este problema.
3. Mala gestión del tiempo
La falta de planificación y priorización puede resultar en retrasos y baja productividad, por lo que hay que implementar técnicas de gestión del tiempo y establecer prioridades claras para mejorar la eficiencia.
4. Problemas con el equipo de manejo
Equipos defectuosos o inadecuados pueden causar accidentes y retrasos. Es crucial realizar mantenimiento regular y asegurarse de que el equipo esté en buen estado de funcionamiento.
5. Falta de seguridad
Esto puede resultar en accidentes y pérdidas, por lo que la seguridad debe ser una prioridad.
6. Mala gestión de inventarios
La falta de control y seguimiento puede llevar a problemas de abastecimiento y exceso de inventario. Utilizar sistemas de gestión de inventarios puede ayudar a mantener un control preciso.
7. Falta de capacitación del personal
El personal no capacitado puede cometer errores que afectan la eficiencia del almacén. Por lo que es importante realizar capacitaciones continuamente y enfocarse en el desarrollo profesional para mantener un personal competente.
8. Problemas de comunicación
La falta de comunicación efectiva entre el personal puede causar malentendidos y errores. Fomentar una comunicación abierta y clara puede mejorar la coordinación y eficiencia.
9. No utilizar tecnología adecuada
La falta de tecnología moderna puede limitar la eficiencia y precisión. Implementar tecnologías como sistemas de gestión de almacenes (WMS) puede mejorar significativamente las operaciones.
10. Problemas con proveedores
Esto puede resultar en retrasos y problemas de abastecimiento. Mantener una buena relación y comunicación con los proveedores es crucial para asegurar un flujo constante de productos.
11. Resistencia a la automatización del almacén
Negarse a adoptar soluciones automatizadas puede limitar el rendimiento y la eficiencia del mismo. Tecnologías como transportadores, transelevadores y carros motorizados pueden mejorar significativamente la logística y transporte, por lo que la automatización puede resolver problemas relacionados con el uso de equipos de manipulación y reducir costos operativos.
Lee también: Trabajar en logística: ¿qué cargo desempeñar si hice una maestría?
¿Qué errores debes evitar en los equipos de manipulación?
1. No realizar mantenimiento regular
Tal como mencionamos, el mantenimiento preventivo es crucial para evitar fallos y prolongar la vida útil del equipo. Además, ayuda a identificar y solucionar problemas antes de que se conviertan en fallos mayores, mejorando así la logística empresarial.
2. Uso inadecuado del equipo
Utilizar el equipo de manera incorrecta puede causar daños y accidentes. Es importante seguir las instrucciones del fabricante y utilizar el equipo de manera adecuada.
3. No actualizar el equipo obsoleto
El equipo antiguo puede ser menos eficiente y más propenso a fallos, por lo que es importante invertir en equipos modernos y actualizados para mejorar la eficiencia y reducir el riesgo de fallos.
4. No seguir las normas de seguridad
Ignorar las normas de seguridad puede resultar en accidentes graves. Es crucial seguir todas las normativas y mejores prácticas para garantizar el buen funcionamiento.
5. Sobrecargar el equipo
Utilizar el equipo más allá de su capacidad puede causar daños y fallos. Así que es importante conocer y respetar los límites de capacidad del equipo.
6. No realizar inspecciones regulares
Estas pueden identificar problemas antes de que se conviertan en fallos mayores. Un programa de inspecciones regulares puede mejorar la seguridad y eficiencia.
7. No tener un plan de contingencia
Es importante tener un plan para situaciones en las que el equipo falle. Un buen plan puede minimizar el impacto de los fallos del equipo.
8. No considerar la ergonomía
El equipo debe ser ergonómico para reducir el riesgo de lesiones al personal para mejorar la comodidad y eficiencia del personal.
Evitar estos errores comunes puede mejorar significativamente la eficiencia y efectividad de tus operaciones logísticas, por lo que si estás interesado en profundizar tus conocimientos y habilidades en este campo, estudia la Maestría en Logística Internacional que tenemos para ti en UMAD para que puedas convertirte en un experto en logística y transporte, y puedas enfrentar los desafíos del sector con confianza y competencia. ¿Qué esperas?